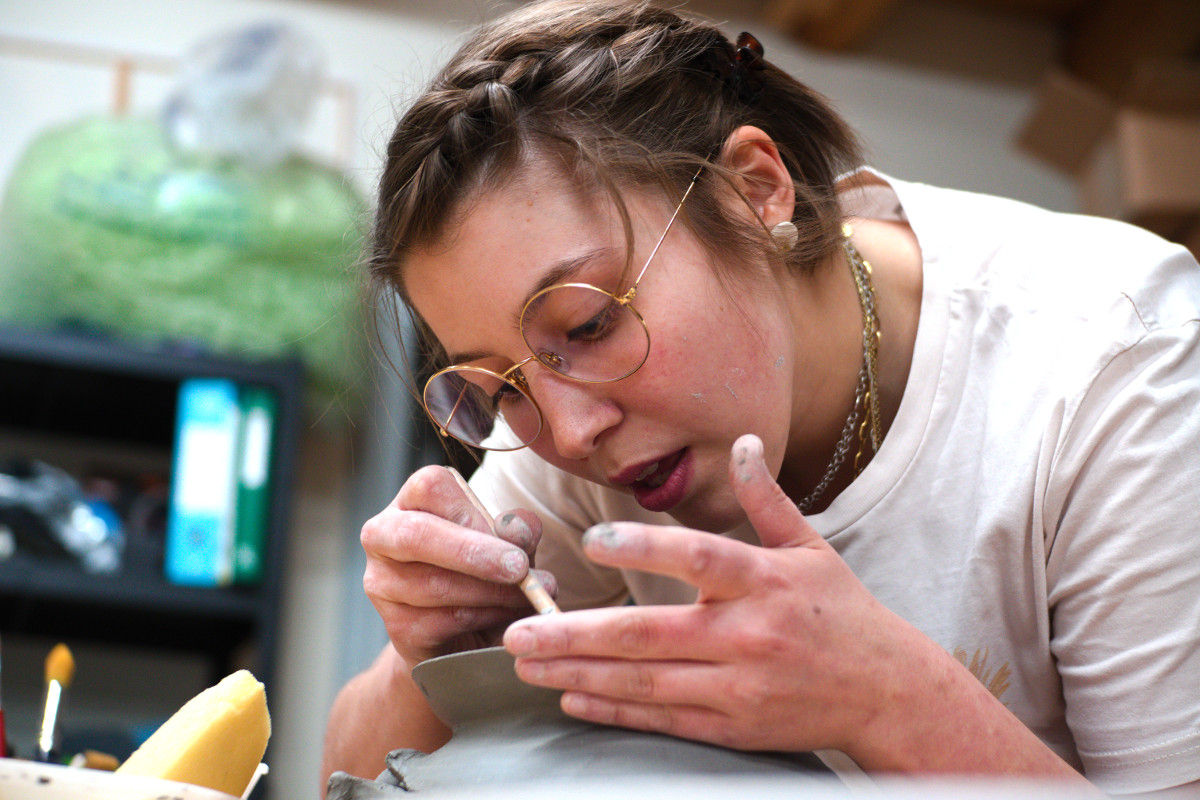
Trust
Craftsmanship differs from industrial production not only in its slower dynamics and smaller volumes, but also and especially in its ethics.
The artisan knows the best way to create an object, unlike the customer, who desires a certain object with certain characteristics, but does not know its production process in detail.
The task of the artisan, then, is to create the object in the best way that his means and experience allow, without compromising his/her ethics, perhaps by producing cheap and poorly created objects in order to lower the price.
The customer, on the other hand, will necessarily have to rely on the artisan, accepting to pay a price that is higher than a similar, industrially produced object, and consciously choosing to establish a relationship of trust, in which he/she recognizes the artisan’s morality, that requires him/her to create the object to the best of his/her ability.
In this sense, the relationship between customer and artisan is not passive, but active, and presupposes open-mindedness and listening on both sides.
Education
Education is crucial in this context: both of the artisan, who educates the customer about production dynamics, and of the artisan him/herself, who constantly studies and learns to improve the quality of his/her production over time.
These are the values I believe in and this is why I chose to become an artisan myself and open my business in 2021. Curiosity about my art drives my hand, while I continuously educate my mind with courses and training.
The richness of education, however, is not in the act of study itself, which can be sterile and an end in itself, but rather resides in the choices it leads us to make.
For all these reasons, in the spring of 2023 I made a radical decision: to change my ceramic production entirely, abandoning all the production dynamics followed until then and launching into a totally new production.
Environmental impact
Two things happened in the spring of 2023: the first was attending the ESG course at the University of Udine. ESG stands for Environmental Social and Corporate Governance, and it indicates business management that not only takes care of the economic aspect of a company, but also takes care of the social and environmental aspects.
The second was reading the book Circular Ceramics by Sara Howard, a British ceramist who created a circular ceramics project, that is, created 100 percent with materials from industrial waste, and documented her research in a book so that other ceramists could follow her example. As a result of these events, I began to inquire about the environmental impact of my production and discovered that this is very high, even at such a modest level as handmade production can be.
The firing temperature of ceramics, for example, is very high (from 1000º to 1250۫ºC) and this involves a high consumption of electricity, while on the other hand the materials, being of mining origin, are extracted from mines and quarries, generating environmental damage, polluting waste and in some cases even serious human rights violations.
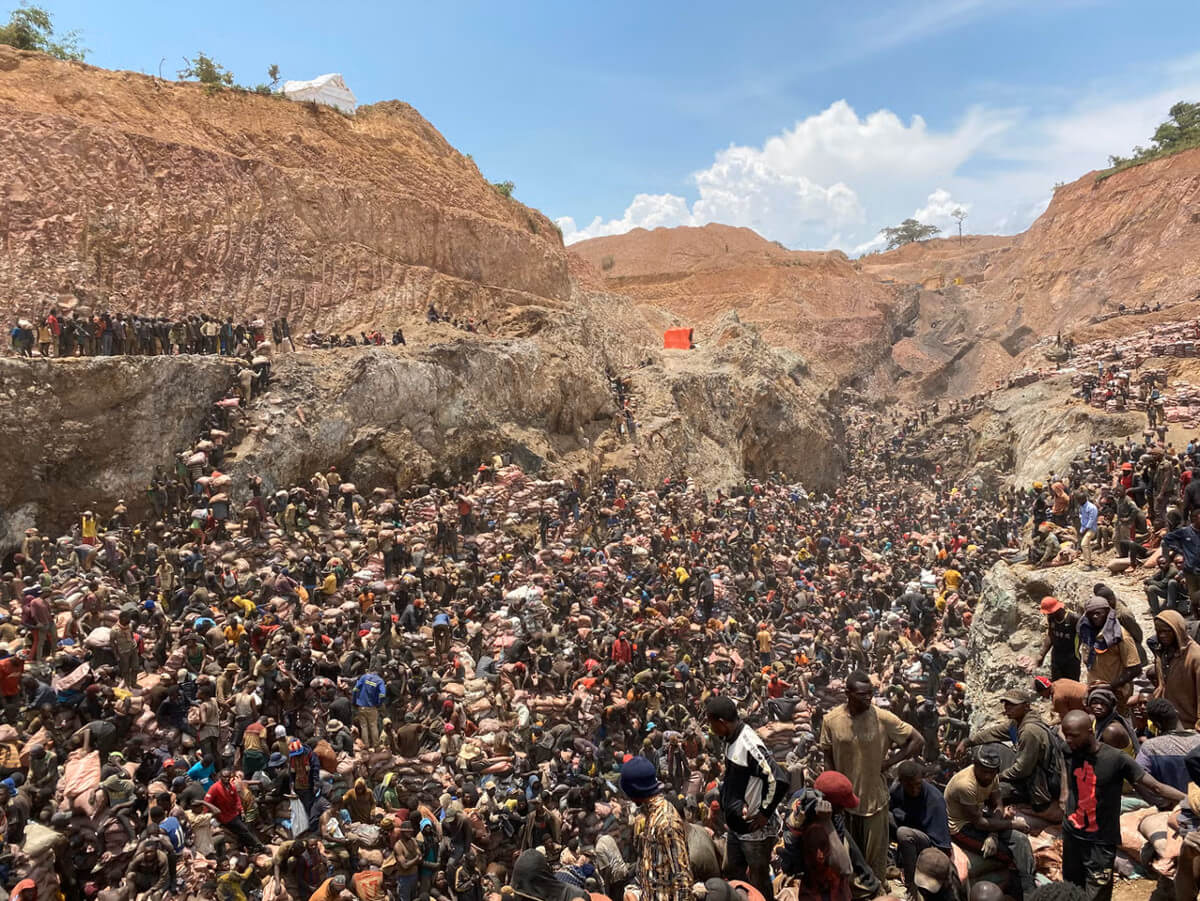
Cobalt
This is the case with cobalt, most of which is mined in the Democratic Republic of Congo, by workers without protective equipment, often children and in slave-like conditions. To date, the nature of the political situation in the Democratic Republic Del Congo makes it impossible to distinguish which batches of material come from ethical mining situations and which from humanitarian risk situations; therefore, no batch of cobalt can be considered 100% ethical.
In the context of ceramic materials, cobalt is used in glazes and pigments to achieve the characteristic “cobalt blue,” but it can also be found in green, turquoise, pink, purple, and black. When I learned this data my production was characterized entirely by products with these colors, moreover, I had just finished an experimental phase that lasted about two years for a new line of products all in shades of blue (see pictures below).
After a long and painful consideration, I decided that it was not acceptable for me to continue the production of products with materials from an unethical supply chain, and I therefore decided to stop buying glazes and products containing cobalt and to start from scratch with a renewed production that was more attentive to the environmental and human impact of the materials I would use.
Consistency
When I began to inquire about the origin of my materials, I was met with some resistance from suppliers; for example, I was told that the exact composition of the clays and glazes is covered by trade secret, and therefore it is not possible to know its specifics.
In addition, when I brought up my concerns about cobalt with my suppliers, I’ve been called a hypocrite, because there are many other metals present in ceramic materials, e.g., lithium, that are extracted under similar conditions, and to date I am still unable to identify in which of my compounds this material is present.
Finally, the violation of human rights is not the only problem related to the ceramic industry: as mentioned above, even just the environmental impact of the industrial production of clay bodies is significant, both because of the damage this extraction can cause to the environment and surrounding communities, and because of the widespread practice of excavating minerals in different geographic areas, and then transporting them to the place where they will be assembled to create a clay or glaze, resulting in heavy environmental impacts due to the transport of these materials.
I am not the only ceramicist concerned about these issues, in fact within the ceramic community there is an increasingly important movement related to the self-production of one’s own materials, extracting them from nature through the search for geological areas with high concentration of clay soils.
Therefore, I decided that I too could pursue this path: however, when comparing opinions with Dr Sergo Valter, professor of ceramic materials at the University of Trieste, the following thought was proposed to me:
“Evaluating the environmental impact of a certain object is a thorny issue; sure, on paper it may look very nice and eco-friendly to make your own clay, but you have to evaluate whether the environmental impact given by the transport of the clay, the use of water and the means used to hydrate and filter it, are actually more sustainable than an industrial production, which employs professionals to optimize its production to the maximum”.
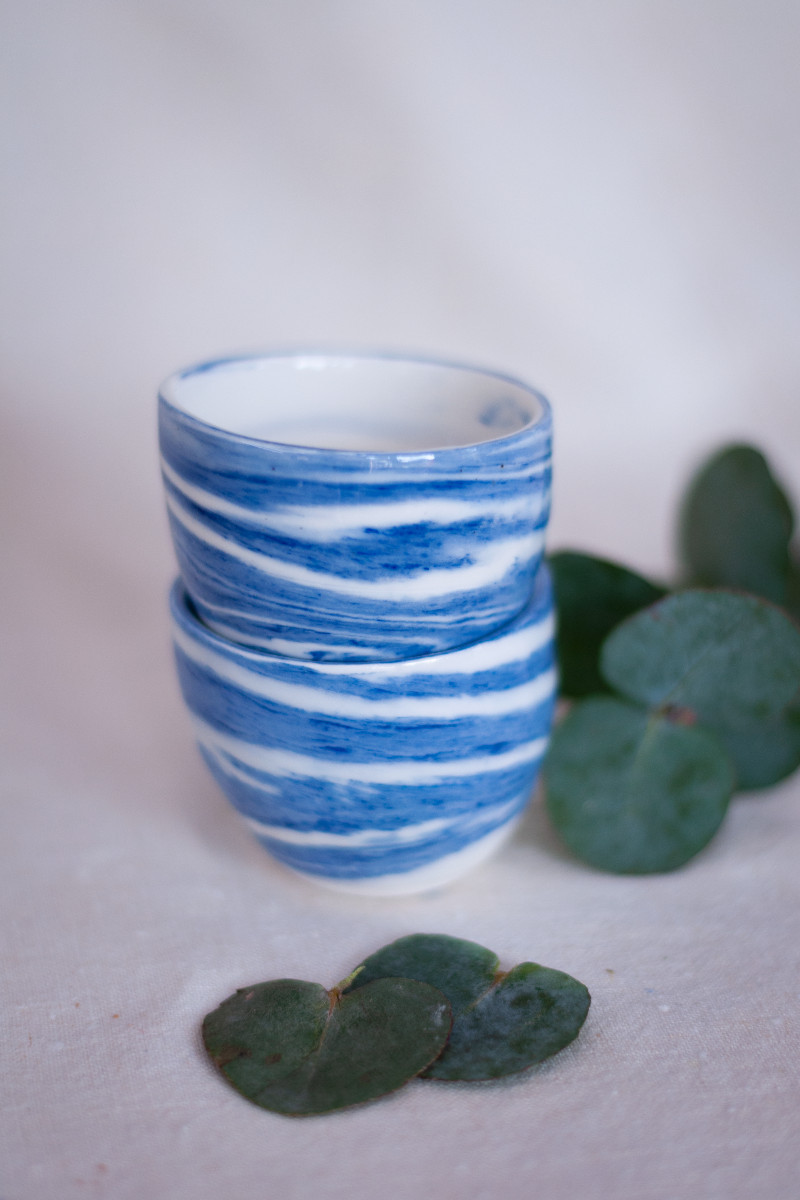
Solution
In light of this data, it is evident that it is very difficult to understand what is ethical and/or sustainable in the field of ceramics, and it could be said that we all move in a “gray zone” with respect to what is right or wrong.
The solution I have adopted was born out of my expertise in the area of the material that I know and work with, but also and more importantly out of my instincts and my personal sense of ethics, therefore I do not claim that my assessments are better than others, or that they are the only correct ones.
On the contrary, I have chosen to present my thought process and research in a completely transparent manner, so that my clients or would-be clients can make an informed decision in complete autonomy, assessing whether or not my sustainability arrangements are appropriate.
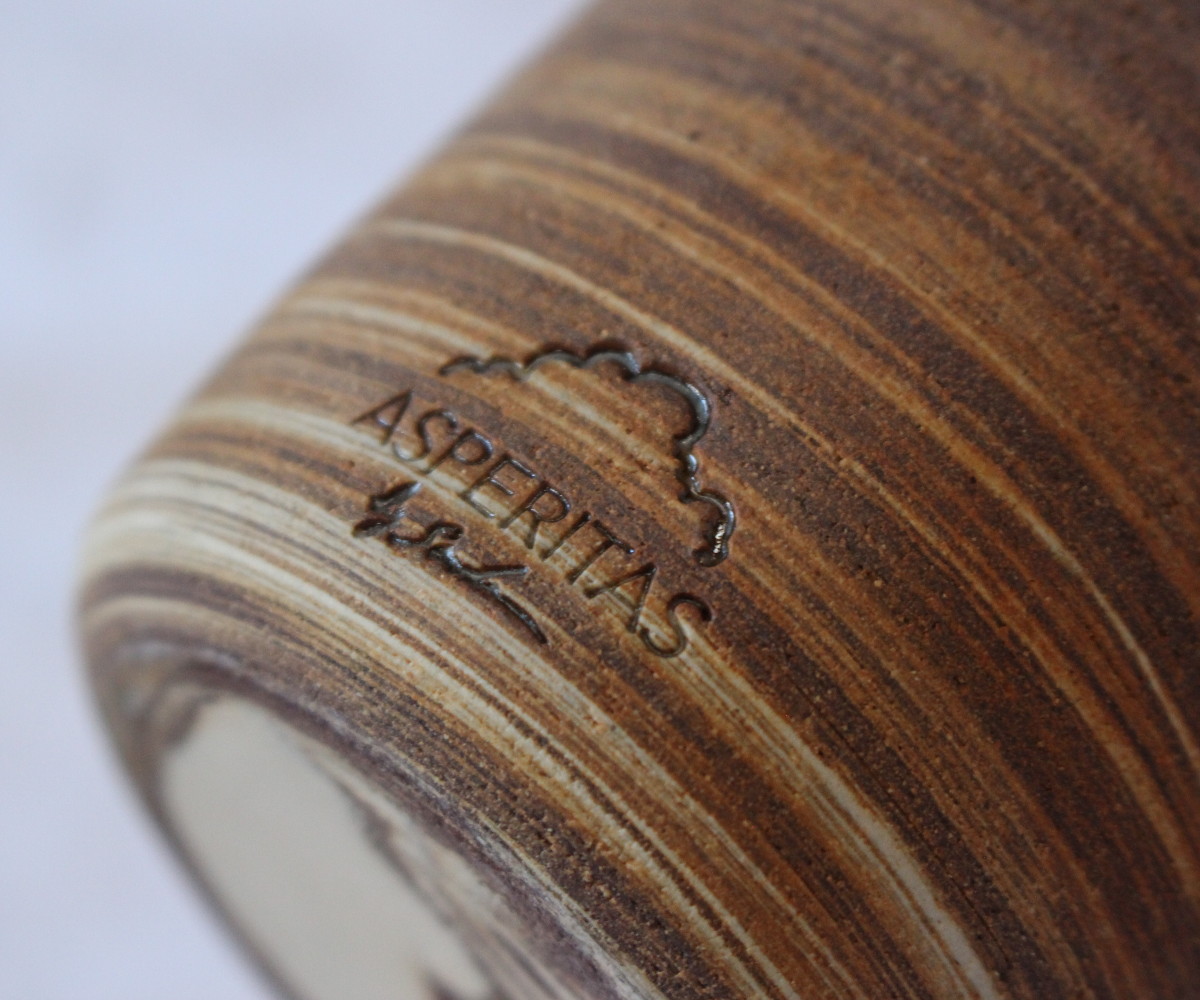
Conclusion
In conclusion, my production now is without coloured glazes or pigments-or rather, it will be once the glazes that were already in the studio are exhausted, as throwing away glazes that were purchased in the past and perfectly functional seemed to me a greater sin than continuing to purchase the ethically “compromised” materials.
I use clays with natural colors given by the presence of iron minerals in the clay body, and to make my artifacts more pleasing to the eye I use the technique of neriage, which consists of mixing together several different clays to give the object a marbled appearance that is unique and unrepeatable.
I have decided to use mainly one glaze, the transparent glaze, to make my tableware more hygienic and simplify its care and washing. This main body of production will be joined by a smaller production branch of wares finished by a white glaze based on barium carbonate and zinc oxide, and some products with gold luster finishes.
Sources:
Circular Ceramics, Sara Howard, 2023
https://www.cobaltinstitute.org/sustainability/cobalt-analysis/
https://www.npr.org/sections/goatsandsoda/2023/02/01/1152893248/red-cobalt-congo-drc-mining-siddharth-kara